By Jennifer Erb
In
2017-03-212017-03-23https://wvuieleaders.com/wp-content/uploads/2016/09/[email protected]WVU IE
200px200px
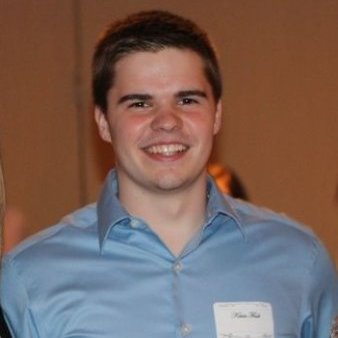
Kevin Fink
IMSE Undergrad Class of 2014
MSA – The Safety Company
What does the company do? Established in 1914, MSA is the global leader in the development, manufacture, and supplier of safety products that protect people and facility infrastructures. With annual revenue of $1.1 billion, MSA employs approximately 4,600 people worldwide across 40 global locations.
Current role: Industrial Engineer II
How I got to my current role:
A day in life of Corporate Finance Professional – My role as an Industrial Engineer with MSA can be broken down into three main functions:
First, I’d like to say that I thoroughly enjoy my job. I work in a fast-paced, constantly changing production environment dealing with hazardous gas detection instruments. At any given time, I am working on 5-10 different projects in a wide variety of professional areas. Some are projects that look like they came from an example in Dr. Byrd’s IE 220 class and some are completely off the wall. At this point in my career, I love those ‘off the wall’ projects. I love challenging myself and trying new projects.
I generally work a 45-50 hour work week, but it varies week to week. Our facility is running 24 hours a day, which means working some very odd hours at times. There is no such thing as a 9AM-5PM day in my role. Sometimes I’ll have an alpha verification build from 3AM – 7AM and then a day full of meetings that last until 4-5PM. Those days are definitely tough, but are not the norm. Other days I’m able to get into work at 7:00AM and be out of the office by 3:30PM. My project work load and priorities dictate my schedule. Below is an example of a recent day I’ve had:
5:30AM – On a normal day, my first alarm sounds at 5:30. I’m usually out of bed around 5:40. I grab a quick shower, breakfast, and coffee to wake myself up for the day.
6:30AM – I wake up my wife and head out to work. My commute is about 30 minutes. This gives me a nice chance to plan out my day and think about what I want to accomplish today.
7:00AM – I arrive at work and check my e-mail for any issues I may need to address. Today I also used this time to run a few financial reports for our management team. I like to get them out of the way early, because they are tedious to run.
8:30AM – My first meeting of the day is a 10 minute Portable Instrument stand up meeting. We discuss how production performed over the past three shifts on Safety, Quality, Delivery, and Cost. The purpose of this meeting is a sanity check on how we’ve done and what we can do better to fix our issues. I generally get an action item or two from this meeting to help maintain our current processes.
8:40AM – Next is a 10 minute Permanent Instrument stand up meeting. This has the same purpose as my first meeting, except for a different production area. After this meeting, I see I am invited to 2 additional meetings this afternoon. So I re-shuffle my schedule to account for the change. This really blows up my plans for the day, but this is a very normal occurrence. My schedule changes on a dime frequently, as is the nature of production.
9:45AM – Next is a 10 minute Industrial Engineering stand up meeting. My colleagues, manager, and I talk about our status on open action items, progress over the past day, and current road blocks. This is a great chance to interface with my manager if I need help on anything.
10:00AM – After my stand up, I jump into a meeting with my co-op on assembly line design for a NPD (new product development) project I am managing. As a mentor to the co-ops, I really try to get their creativity flowing and allow them the freedom to think outside the box. I spend most of the meeting listening to her ideas and giving open feedback on how we can improve the design. I try to guide her to a successful line design, without just giving her all the answers.
10:45AM – I meet with another co-op to give a mid-semester review. I use our time to give him open and honest feedback on his work and professional skillset. We spend most of our time reflecting on his semester so far and discussing road blocks. I finished the meeting by asking for some feedback on how I can perform better as his supervisor.
11:30AM – My next meeting was on another NPD project. We are getting very close to launching this product to the market. This meeting was to review our launch readiness and discuss remaining project risks, action items, and expected completion dates. I was the low guy on the totem pole in this meeting. There were quite a few upper/middle management professionals, which can be nerve-wracking, but is a great opportunity to impress key project stakeholders.
12:30PM – I stop to grab a quick lunch and reset for the afternoon.
1:00PM – I have another meeting on launch readiness (for the NPD project I met on at 10AM) with more upper/middle management professionals. We are several months from launching this product. However, my facility layout design is the critical action item to launch readiness. Basically, my line design project is what’s holding up our team from launching the product. It’s never fun to be in the critical path of a project, but it happens. I communicate openly on my status and expected completion on a high level. Being open and honest is key here. People may not like what you have to say, but they do respect your honesty.
2:00PM – A software problem arises during product testing of a new product. Our software engineers come up with a fix, but they will need production associates to re-program our pre-built inventory. I immediately drop everything and coordinate resourcing and timing to execute this request ASAP.
3:00PM – I lead a meeting with my project team (engineers, supervisors, etc…) on the NPD project that came from the 10AM and 1PM meetings. I covered our scope of work and project plan to get our facility layout prepared for launch on a detailed level. We talked about risks and scope feasibility, really digging into any potential plan gaps. From here, I can make any revisions to help me more effectively manage my facility layout plan.
3:30PM – I finally get back to my desk, I haven’t been here since 9ish this morning. Thankfully, I have been able to check and respond to e-mails throughout the day. I finish responding to e-mails I haven’t addressed yet.
4:00PM – I meet with my manager for a weekly one-on-one to review my projects, bandwidth, and career development goals.
4:45PM – Time to call it quits and head home.
Why choose production IE? My job is fast-paced, ever changing, and always challenging. I get to see my projects go from a concept on the back of a napkin to a fully developed system or assembly line. I am responsible for my own success and I have earned the freedom to drive my own ideas and projects. I am a leader of projects, people, and processes. With that responsibility comes stress, but there is nothing more fulfilling than making a difference in my company. I can honestly go home every night knowing that I have made a huge difference at MSA through my role.
What’s the end goal? My end goal is to become an operations project manager. After researching the many different corporate paths, I feel that project management fits my personal style, and I believe I will be happy in the role. From there, I aim to become a director, supervising project managers.
Most surprising thing that I didn’t expect coming out of college – I always thought that being successful in my career meant focusing on how to be a great IE. I was completely wrong. The key to success is learning how to be a leader within your group, team, and company regardless of your position. The ability to lead is a transferable skill set that is crucial to any position. I believe having this ability in addition to a sound technical skill set will help any professional to be successful in their role.
My Advice – Always remember that work is more than just a paycheck. Take pride in what you do. Make a difference. Always challenge yourself and learn. And most importantly, do what makes you happy and enjoy your work.